3D printing meets CNC machining: new gripper for tire testing systems
Sectors • Published on: 9/24/2024
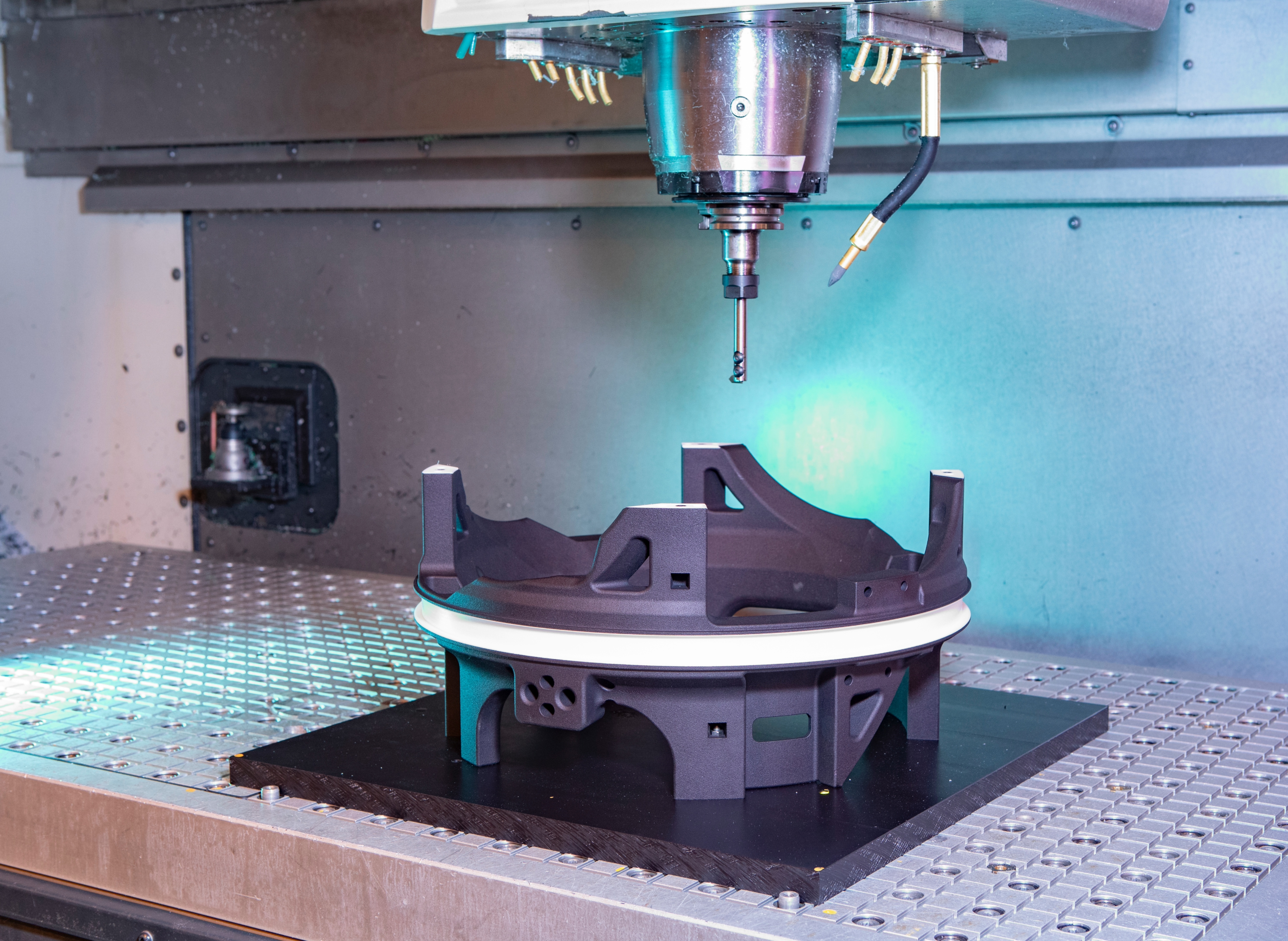
At Murtfeldt, we combine modern technologies and materials to solve complex challenges efficiently. Our current project: A gripper for tire testing systems that sets new standards through the fusion of 3D printing and CNC machining.
The challenge
The previous solution - a simple steel construction - had reached its limits. Higher weight and precision requirements led to frequent system downtimes. To solve this problem, we developed a hybrid solution that optimally combines lightweight construction, precision and functionality.
Technology fusion for maximum performance:
The new gripper was manufactured in Kusterdingen at Murtfeldt Additive Solutions using the selective laser sintering (SLS) process and utilizes the full design possibilities of 3D printing. This enabled a geometry that would not be possible with conventional manufacturing - a clear advantage in terms of lightweight construction and functionality. The aluminium body of the gripper also ensures cost optimization, while the subsequent CNC machining in Dortmund guarantees maximum precision.
Our solution
By merging our 3D printing and CNC machining technologies in the Murtfeldt Group, we were able to create a complex component that would not have been possible with just one of the technologies. This hybrid approach enables us to develop products with improved geometry that not only increase the efficiency of the tire testing system, but also reduce system downtime - a clear advantage over conventional solutions.
Partnership and looking to the future
The close cooperation between Murtfeldt Additive Solutions and Drehmoment has existed for several years. Short communication channels and quick access to the right contact persons enable such projects to be implemented quickly. In addition, Drehmoment gives us access to other customers.
Our joint expertise within the Murtfeldt Group in 3D printing and processing plastics was the key to our success. In the future, we will continue to work on optimizing the gripper and other hybrid components in order to be able to offer our customers tailor-made and innovative solutions.
You might also be interested in
New dimensions in 3D printing
At our site in Kusterdingen, we have built a helicopter for flight training from a total of 13 additively manufactured components...